Tips on Pump Mechanical Seal Maintenance
Author:admin Date:2023-05-24
When it comes to maintaining your pumps, it is important to replace the Pump Mechanical Seal whenever possible. Whether it's the lubrication or the seal itself, you should make sure to follow all manufacturer guidelines to maintain the performance of your pumps. By following these tips, you can ensure that your pumps will continue to function safely for years to come. Listed below are some tips on pump mechanical seal maintenance. If you notice any irregularities, contact your local manufacturer's representative for assistance.
A Pump Mechanical Seal consists of a stationary and rotating face ring. This assembly must be sealed to the shaft and housing to prevent leaks. Secondary seals typically include elastomer O-rings or boots. These seals are a simple way to protect your pump from fluid damage. The main purpose of a Pump Mechanical Seal is to keep your pump running efficiently. A mechanical seal is designed to prevent leaks and prevent overheating.
High-pressure pumps often use buffer space seals to avoid high-pressure problems. Boiling water reactors run at up to 170 bar, and a buffer space seal enables a pump to operate safely at lower pressures. Boiler circulating pumps, for example, operate at up to 170 bar. A series arrangement of three seals allows each to operate at one-third the pressure and maintain a seal life of 15 years.
Dual-sealing pumps often incorporate a buffer fluid or barrier fluid to prevent leakage of the pumped liquid. This type of pump mechanical seal is a backup for the primary seal and may also serve as a containment system. An external reservoir provides the buffer fluid for the outer seal. The internal pumping ring maintains circulation in the chamber during normal operation. The buffer liquid is typically continuously vented to a vapour recovery system.
The pump mechanical seal supports the entire system and is integral to proper functioning. Properly functioning mechanical seals help maximize efficiency and reliability of pumps. Most repairs occur due to problems with the mechanical seal, so it is imperative to have a high-quality mechanical seal support system. The KSB mechanical seals impress with robust design and excellent integration in the seal chamber. These mechanical seals are the best solution for your centrifugal pumps.
Mechanical seals are manufactured with stationary and rotating seal faces. The stationary face is typically made of carbon, and the rotating face is typically a hard material. Carbon is available with a variety of binders, including acetone and silicone. In addition to this, a mechanical seal can be used in compressors. As a general rule, mechanical seals are suitable for a wide range of temperatures and operating speeds. The temperature capability of the seal depends on the secondary seal and the combination of stationary and rotating faces.
The design of a mechanical seal can differ. It consists of two seal faces - one connected to the rotating shaft and the other to the stationary casing. A thin fluid film between the two faces acts as lubricant, preventing excessive wear on the sealing surfaces. A process fluid is typically used for pump mechanical seal applications. It is important to understand how these seals work and what the benefits and risks are before choosing one for your application.
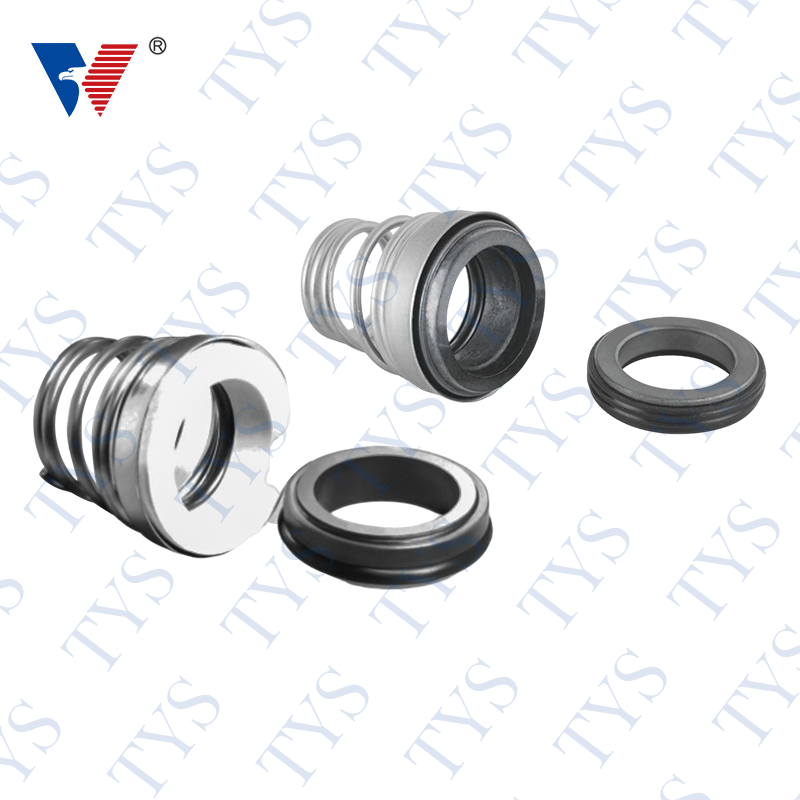
TYS 155 Single spring mechanical seals for water pump seal
Annular Seal Pressure: ≤0Mpa~0.8Mpa
Annular Seal Temperature: -20~ 80℃(-30~200℃)
Rotation speed:≤12m/sec
Medium: Water, Oiland PH numerical value of waste water is 6.5-8
Used in clean water pumps and circulation pumps.
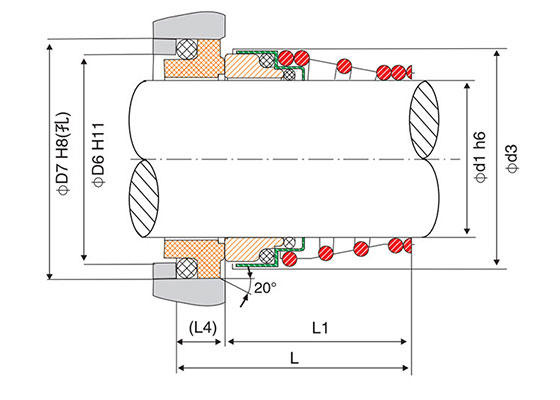