Precision and Reliability: The Art of Mechanical Seal Manufacturing
Author:admin Date:2023-07-07
In the realm of industrial engineering and fluid handling systems, mechanical seals are vital components that ensure the integrity and efficiency of rotating equipment. The manufacturing process of mechanical seals combines meticulous craftsmanship with advanced technology to create precise, reliable, and robust sealing solutions.
Understanding Mechanical Seals
Mechanical seals are devices used to prevent leakage between two mating surfaces in rotating equipment, such as pumps, compressors, and mixers. They consist of several key components, including stationary and rotating faces, secondary sealing elements, springs, and retainers. When properly designed and manufactured, mechanical seals provide a secure and long-lasting seal, preventing fluid leaks and ensuring the efficient operation of machinery.
Manufacturing Process
1. Design and Engineering: The manufacturing process begins with detailed design and engineering. Engineers carefully analyze the specific requirements of the application, considering factors such as pressure, temperature, fluid type, and operating conditions. Advanced computer-aided design (CAD) software is employed to create precise 3D models that serve as the foundation for manufacturing.
2. Material Selection: Mechanical seals are manufactured using a wide range of materials, including metals, ceramics, carbon, and various elastomers. The choice of materials depends on the application requirements and the fluids being sealed. Each material must exhibit the necessary properties such as chemical resistance, wear resistance, and compatibility with the mating surfaces.
3. Precision Machining: Precision machining plays a crucial role in mechanical seal manufacturing. Computer numerical control (CNC) machines are utilized to achieve high levels of accuracy and consistency. The components of the seal, such as the faces, springs, and retainers, are machined to tight tolerances to ensure proper fit and functionality.
4. Assembly and Testing: The individual components are meticulously assembled to create the complete mechanical seal. Skilled technicians carefully follow assembly instructions, ensuring proper alignment and installation of all components. Once assembled, the seals undergo rigorous testing to verify their performance under various operating conditions. Leakage, pressure, and temperature tests are conducted to ensure the seals meet the required specifications.
Quality Control Measures
Manufacturers of mechanical seals employ stringent quality control measures to ensure the reliability and performance of their products. These measures include:
1. Material Testing: Incoming materials are subjected to thorough testing to verify their quality and conformance to specifications. This includes chemical analysis, hardness testing, and mechanical property evaluations.
2. Dimensional Inspection: Each component undergoes dimensional inspection to verify adherence to design specifications. This is done using precise measuring instruments such as coordinate measuring machines (CMMs) to ensure proper fit and functionality.
3. Performance Testing: Completed mechanical seals are subjected to performance testing under simulated operating conditions. These tests include leakage testing, endurance testing, and performance verification at different speeds, pressures, and temperatures.
4. Traceability and Documentation: Manufacturers maintain detailed records and documentation throughout the manufacturing process, ensuring traceability and accountability. This enables the identification and resolution of any issues that may arise during production or in the field.
Understanding Mechanical Seals
Mechanical seals are devices used to prevent leakage between two mating surfaces in rotating equipment, such as pumps, compressors, and mixers. They consist of several key components, including stationary and rotating faces, secondary sealing elements, springs, and retainers. When properly designed and manufactured, mechanical seals provide a secure and long-lasting seal, preventing fluid leaks and ensuring the efficient operation of machinery.
Manufacturing Process
1. Design and Engineering: The manufacturing process begins with detailed design and engineering. Engineers carefully analyze the specific requirements of the application, considering factors such as pressure, temperature, fluid type, and operating conditions. Advanced computer-aided design (CAD) software is employed to create precise 3D models that serve as the foundation for manufacturing.
2. Material Selection: Mechanical seals are manufactured using a wide range of materials, including metals, ceramics, carbon, and various elastomers. The choice of materials depends on the application requirements and the fluids being sealed. Each material must exhibit the necessary properties such as chemical resistance, wear resistance, and compatibility with the mating surfaces.
3. Precision Machining: Precision machining plays a crucial role in mechanical seal manufacturing. Computer numerical control (CNC) machines are utilized to achieve high levels of accuracy and consistency. The components of the seal, such as the faces, springs, and retainers, are machined to tight tolerances to ensure proper fit and functionality.
4. Assembly and Testing: The individual components are meticulously assembled to create the complete mechanical seal. Skilled technicians carefully follow assembly instructions, ensuring proper alignment and installation of all components. Once assembled, the seals undergo rigorous testing to verify their performance under various operating conditions. Leakage, pressure, and temperature tests are conducted to ensure the seals meet the required specifications.
Quality Control Measures
Manufacturers of mechanical seals employ stringent quality control measures to ensure the reliability and performance of their products. These measures include:
1. Material Testing: Incoming materials are subjected to thorough testing to verify their quality and conformance to specifications. This includes chemical analysis, hardness testing, and mechanical property evaluations.
2. Dimensional Inspection: Each component undergoes dimensional inspection to verify adherence to design specifications. This is done using precise measuring instruments such as coordinate measuring machines (CMMs) to ensure proper fit and functionality.
3. Performance Testing: Completed mechanical seals are subjected to performance testing under simulated operating conditions. These tests include leakage testing, endurance testing, and performance verification at different speeds, pressures, and temperatures.
4. Traceability and Documentation: Manufacturers maintain detailed records and documentation throughout the manufacturing process, ensuring traceability and accountability. This enables the identification and resolution of any issues that may arise during production or in the field.
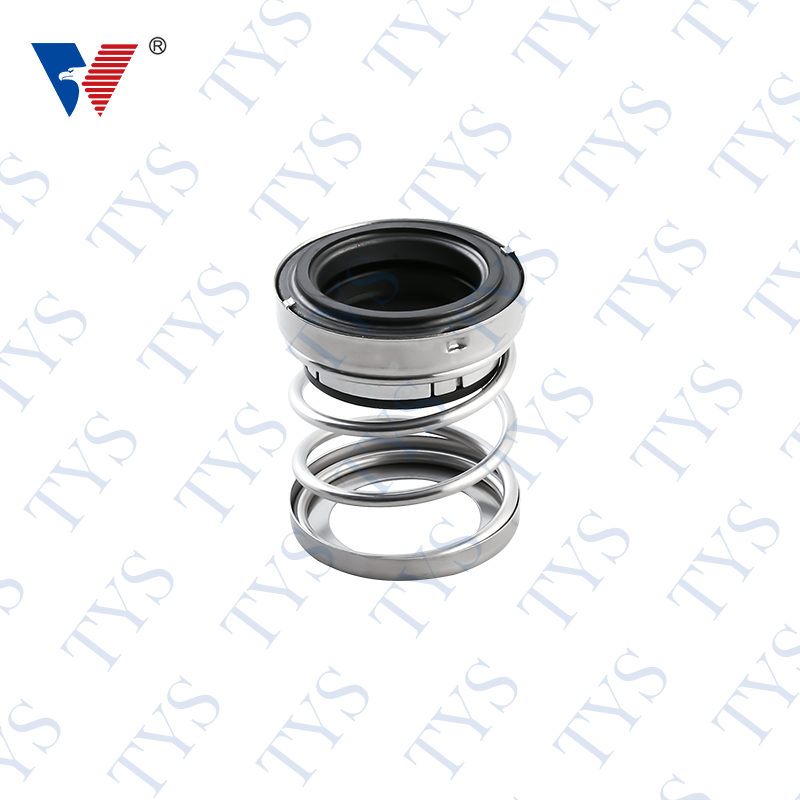